CHEAP IMITATIONS OF BLACKMER
® TX SERIES TRANSPORT PUMPS MAY HAVE A LOWER UPFRONT COST, BUT LAB TESTS SHOW KNOCKOFF PUMPS RESULT IN INCREASED MAINTENANCE, REPLACEMENT AND DOWNTIME COSTS
By Thomas L. Stone
Introduction
There is no shame in thinking that the product you produce is the best for your particular market. No one who decides to create anything – from cell phones to microwaves, skateboards to luxury automobiles – does so with the idea that they would be happy if the final product turned out to be just “OK.”
When a manufacturer does hit a bullseye in terms of design, performance, reliability and demand, it is only natural that others would want to try and copy that design and capitalize on the product’s popularity and reputation in the market. That’s where it becomes tricky for the end user. While the developer of the so-called “knockoff” version can say that the product is as good as the original, it’s best to keep in mind the old saying that, “If something appears too good to be true, it probably is.”
That bromide is definitely relevant in the world of industrial pumps. Over the years, creative, forward-thinking pump manufacturers have produced a wide range of pump technologies, styles and models that have come to be recognized as leaders in their field. In the realm of fluid transfer, the sliding vane pump has proven for more than a century that it is a go-to technology for the handling of oils, fuels and other valuable liquids.
Within that niche, sliding vane pump technology has emerged as one of the preferred choices for transport companies that operate fleets of trucks used for the delivery of chemicals, petroleum products and other industrial liquids. Sliding vane pumps are a wise choice in these applications because their design and method of operation allow them to meet the demands that are put on truck-mounted transport pumps, including quiet, trouble-free operation; dry-run and self-priming capabilities; efficiency in handling a wide array of fluids; and easy maintenance.
Making The Case
Naturally, because of the success of sliding vane pumps in the transport market – and the standard-setting operation of the technology’s leading manufacturers – in recent years a number of offshore imitators has surfaced, many of which are based in China, India and other developing countries. The sales pitch of these imitators revolves around a promise that their pumps are just as good as the original, but with a lower purchase price.
After assessing the effects that the arrival of the knockoff pumps could have on its standing in the transport market, Blackmer
®, Grand Rapids, MI, USA, a product brand of PSG
®, Oakbrook Terrace, IL, USA, a Dover company, commissioned side-by-side tests that pitted its TX Series sliding vane pumps against several offshore knockoff brands. The eye-opening results showed that the operation of the knockoff pumps, as well as their critical components, do not measure up in terms of quality and durability to the standard that the TX Series sliding vane pump has set.
Specifically, the Blackmer pumps proved to perform better than the competition in the following areas:
• Flexural Strength: Side-by-side comparisons revealed that the vanes in a TX pump outperformed competitive models by more than a two-to-one ratio when measuring flexural strength. The TX vanes can withstand pressures up to 25,813 psi (1,780 bar), while Competitor A’s flexural strength topped out at 11,174 psi (770 bar) and Competitor B’s was only slightly better at 11,988 psi (827 bar).
• Operational Capabilities: The comparison test set the operational service pressure at 150% of the pump’s rating, or 225 psi (15.5 bar) at 640 rpm. Under these operating conditions, the competitor’s pump broke down after only 50 hours of use, while the TX pump exceeded 250 hours of operating time under the same conditions.
• Relief Valve Operation: The relief valve on two knockoff models did not open properly, which allowed the internal pressure of the pump to reach more than 200 psi (13.8 bar). When internal pump pressures are allowed to get this high, the system can be destroyed with catastrophic (and dangerous) failures of hoses, meters and nozzles.
• Part Reliability: The manufacturers of knockoff pumps are able to offer a lower price because they may use components that are not as robust as those on the standard model. For instance, the lock nuts on the tested knockoff pumps are smaller and have a looser tolerance than those on the TX pumps. This is important because a tight fit prevents slippage and keeps all components in perfect alignment. This helps ensure reliable operation every time the pump is run.
• Noise Suppression: Tested at a differential pressure of 122 psi (8.4 bar), the TX pumps produced airborne noise at a rate of 77 decibels, while the knockoff models had airborne noise approaching 90 decibels, or the equivalent of a newspaper press.
Closing The Case
These documented and verified results should effectively make the case that knockoff versions of industry-standard pumps that are making their way into the market are incapable of replicating the performance, durability and reliability of what has become the leading technology.
While the results undoubtedly highlight the superiority of the TX pumps, end users may still be tempted by the lure of the knockoff brand’s main call to action: the modestly lower purchase price. It’s true that upfront cost savings can be tempting, especially for companies where budgets are tight and the need to be conservative in expenditures is a key component in operating the business.
So, to many the lower purchase price can become the determining factor when choosing between the industry standard and the one that claims to deliver comparable performance with a reduced monetary outlay. In these situations, it’s best to weigh the upfront gains with the potential for increased costs on the back end. Namely – and as proven by the side-by-side comparison tests – settling for a knockoff model may often deliver upfront savings that will be quickly mitigated once the pump is put into service.
For instance, vanes that don’t possess adequate flexural strength, relief valves that don’t function properly or reliably and parts that are not as robust as the industry standard are more likely to wear out or break down faster. When these inevitable operational woes occur, the only logical result is higher costs for maintenance, repair, replacement parts and, in the worst-case scenario, an unexpected cash outlay for a new pump. The hidden cost in these situations is the downtime that is incurred as a truck that sits idle because a pump needs to be repaired or replaced. Simply put, a truck that is not completing the deliveries that are the lifeblood of, for example, a heating-oil delivery company is a drain on the company’s bottom line.
An offshoot of the downtime that can stall the delivery schedule is something that can be just as costly for the delivery company: a loss of reputation. The company that cannot consistently and reliably get that heating oil into the tank of the consumer and ready for use on those cold winter mornings is not one that will be in business for very long. In other words, the reputation of the company itself is worth much more than the negligible amount of up-front money that might be saved when a knockoff is purchased instead of the industry standard.
Blackmer has consolidated the results of the comparison tests and the other ways in which its TX Series pumps will outperform knockoff brands on its “TX Strong” website, located at blackmer.com/txstrong.
Conclusion
Everyone has been tempted to buy the cheaper version of an industry-standard product, but many times the purchaser ends up getting burned. A lower cost alternative may produce slight monetary benefits up front, but when the knockoff pump breaks down, the rise in maintenance, repair and replacement costs, coupled with the downgrade in reputation and erosion of customer loyalty can have far-reaching effects that will far outweigh the initial cost of the pump.
About the Author:
Thomas L. Stone is the Director of Marketing for Blackmer
® and PSG
®. He can be reached at
tom.stone@psgdover.com. For more information on Blackmer’s full line of pumps and compressors, please go to
blackmer.com or call (616) 241-1611. Blackmer is a product brand of PSG
®, a Dover company, Oakbrook Terrace, IL, USA. PSG is comprised of several of the world’s leading pump brands, including Abaque®, Almatec®, Blackmer
®, Ebsray
®, EnviroGear
®, Griswold
™, Mouvex
®, Neptune
™, Quattroflow
™, RedScrew
™ and Wilden
®. You can find more information about PSG at
psgdover.com.
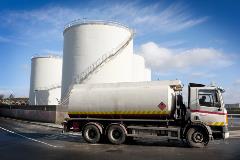
Uptime is the lifeblood of the transport industry as fleet vehicles that are idled are a drain on the transport company’s bottom line. Keeping the wheels rolling requires the use of the best components, including the transport pumps that facilitate deliveries. Successful fleet managers rely on proven, best-in-class technology like TX Series Sliding Vane Pumps from Blackmer
® and are wise to shun cheap knockoff imitations that may have a lower upfront cost, but will result in increased maintenance, replacement and downtime costs.
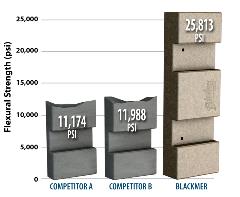
Pressure is great for forming diamonds, but it can wreak havoc on pump components. Side-by-side comparisons have confirmed that Blackmer sliding vanes outperform competitive models by more than two-to-one in flexural-strength tests.
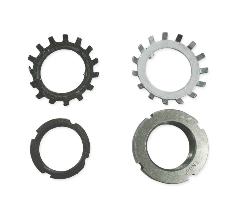
A tight fit prevents slippage and keeps everything running in perfect alignment. Blackmer’s lock nuts are carefully machined for a perfect fit every time.
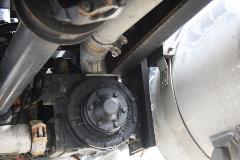
In side-by-side tests with knockoff pumps, Blackmer
® TX Series Sliding Vane Pumps clearly outperformed the competition in vane flexural strength, operational capabilities, relief-valve operation, part reliability and noise suppression, making them the clear choice for transport-fleet managers.
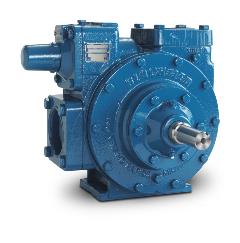
For more than 100 years, Blackmer has been building pumps in Grand Rapids, MI, USA. They’re proven in the harshest conditions - and side-by-side tests now show that they are the obvious choice over the cheap knockoff imitations that have begun to enter the transport market.