WHILE CENTRIFUGAL PUMPS HAVE TRADITIONALLY BEEN A GO-TO TECHNOLOGY IN THIS INDUSTRY, THE MANY OPERATIONAL ADVANTAGES OF SCREW PUMPS CAN MAKE THEM A PRACTICAL ALTERNATIVE
By Josh Pepper
Introduction In the industrialized world, there may be no more deceptively named mode of transportation than the “very large crude carrier,” or VLCC. Calling an oil tanker that can be nearly half a kilometer in length “very large” is akin to saying that King Kong is a “pretty big” gorilla or that the Great Wall of China is “kinda long.”
In reality, the VLCC – along with its “supertanker” cousin, the somewhat more appropriately named “ultra large crude carrier” (ULCC) – plays a, no pun intended, “large” role in the transportation of crude oil and refined petroleum-based products around the globe. The crude-carrying capacity of a VLCC can range from 160,000 to 320,000 dead weight tons (DWT), with ULCCs able to accommodate upwards of 550,000 DWT in one trip.
In fact, some VLCCs and ULCCs are so massive that they cannot enter the actual port. In this case, they must anchor to a floating single-point mooring (SPM) buoy or jetty that is located several kilometers offshore and offloaded there. The SPM is connected to the port by sub-sea pipelines that are capable of handling extremely large quantities of liquid and gas cargo. Using SPMs can also save time and fuel for the operator since the tanker will not be required to enter and maneuver around the port.
While hundreds of VLCCs and ULCCs move millions of barrels of crude oil at a time to the world’s oil refineries, a fleet of product tankers, with capacities of up to 60,000 DWT, stand ready to transport the petroleum, petrochemicals and other refined petroleum products to other pivotal points along the production and supply chain. In other words, there are a whole lot of large ships loaded with crude oil and refined products traversing the world’s oceans, seas and rivers at any one time.
That also means that there are vast quantities of crude-based fluids that must be loaded onto, unloaded off of or transferred between the various classes of VLCCs and ULCCs, product tankers and barges that crisscross the petroleum-products transportation lanes. Traditionally, centrifugal pumps have been a go-to technology that shipbuilders have utilized on their vessels for various fluid-transfer applications. This white paper, however, will show how an oftentimes overlooked pumping technology – positive displacement twin- and triple-screw pumps – can be a more versatile, reliable and efficient alternative to centrifugal pumps in the critical loading/unloading and transfer operations on the vessels that carry crude oil and finished petroleum-based products for the long-haul shipping industry.
The Challenge
The most obvious challenge – and perhaps the toughest to eliminate – in making screw pumps a front-of-mind option for shipbuilders is convincing them to wean themselves off of a technology that has become defined as the best one for a variety of unique fluid-handling tasks. Generally speaking, the bulk of the fluids that are handled on ships, tankers and barges must be transferred at very high flow rates and volumes, which hits the operational sweet spot of centrifugal pumps.
Because of the success of centrifugal pumps in these types of operations, the fluid-transfer systems that have been created by shipbuilders have been designed around the pumping technology, rather than the other way around. This means that engineers who are familiar and comfortable with centrifugal pumps will make every attempt to work within their operational limits. They know how centrifugal pumps operate, know their benefits and are confident that they are still the best technology for all of their many fluid-transfer needs.
To illustrate this state of mind, in some cases a design engineer – instead of even considering an alternative pumping technology – will blend or heat the liquid that needs to be transferred as a way to manipulate the process and get the viscosity of the fluid down to less than 300 cSt, which makes it easier for the centrifugal pump to transfer the fluid. What they are doing in this instance is reconditioning the fluid to fit the pumping technology – without regard to any potential bottom-line cost impact.
In other words, when measures like this are taken to satisfy the operational characteristics of the pump, the popularity of centrifugal pumps for fluid-transfer applications in the shipping industry becomes something of a self-fulfilling prophecy.
Despite the ability to recondition the fluid to meet the operational needs of the centrifugal pump, care must still be taken to ensure that the centrifugal pump is operating at or close to what is known as its “Best Efficiency Point,” or BEP. The BEP is the point where the centrifugal pump is working at its highest level of efficiency. Centrifugal pumps rarely operate at their exact BEP because pristine pumping conditions are rarely encountered, but a centrifugal pump that is able to function in a window that is between 80% and 110% of its BEP is said to be operating within a tolerable range for efficiency.
However, when the operation of the pump moves too far off its BEP uneven pressure will be applied to the impeller, which can result in increased radial thrust that will cause the pump’s shaft to “deflect.” When this deflection occurs, higher loads will be placed on the bearings and mechanical seal, which can lead to damage to the pump’s casing, back plate and impeller. Because of these potential operational hazards, ensuring that the pump is working within an acceptable BEP range can be a time-intensive task since the pump must be monitored constantly and adjusted as needed, which costs time and money.
Regardless of the flow rates and volumes that must be achieved, there are other considerations the shipbuilder must contemplate before deciding on the best pump technology, including:
• A limited footprint on or below decks for installing pumping equipment
• Intermittent service that requires quick, multiple starts with minimal line priming
• Varied shipping media with differing fluid-handling characteristics
• Effective stripping of cargo holds to maximize deliverable working volume while managing gas entrainment without the threat of pump shutdown due to vapor locking
• Strict cycle times regarding incoming and outgoing shipments, with any delays or shutdowns resulting in the incurrence of prohibitive charges or financial penalties that can reduce the shipping company’s profitability
• Level of risk for an explosion due to static charge buildup during filling cycles
The Solution
As mentioned, the solution to the operational disadvantages of centrifugal pumps can be positive displacement (PD) screw pumps. The difficulty in moving screw pumps to the forefront in the minds of shipbuilders is not only overcoming the strong customer familiarity with centrifugal pumps, as evidenced by their sizeable installed base, but in getting design engineers to acknowledge or even become aware that there are alternatives like screw pumps.
In a lot of cases, many engineers are not taught about screw pumps in their studies, and many who are aware of them have a preconceived notion of their supposed shortcomings, or that they are nothing more than lube pumps capable of handing only low flow rates. In reality, today’s screw pump models can offer remarkable advancements in terms of the flow-rate volumes that they can handle, with flow ranges from 220 gpm (833 L/min) to 11,000 gpm (41,635 L/min) not uncommon.
In truth, the design of PD screw pumps makes them capable of handling liquids with varying levels of viscosity – even the thicker raw crude oil that is the bread-and-butter commodity for VLCCs and ULCCs. The screw pump’s operating principle sees opposed screws engaged to form a sealed cavity with the surrounding pump casing. As the drive screws turn, the fluid is conveyed steadily and constantly to the discharge port of the pump, which creates a volumetrically consistent flow rate regardless of the pumping pressure.
The list of benefits provided by screw-pump technology in shipping fluid-handling applications is a long and impressive one:
• A compact design that can be mounted in a vertical or horizontal orientation with minimal deck support while providing a good power-to-density ratio and smooth or nearly pulse-free fluid transfer
• Ability to strip residual fluids from the cargo hull
• Ability to handle a wide range of flows, pressures, liquid types and viscosities without the need to manipulate a BEP position
• No need to pre-heat fluids as high-viscosity fluids can be easily handled without sacrificing performance
• Constant flow, even in the presence of varying system backpressures due to viscosity changes
• Ability to accommodate significant turndown ratios when controlled by an adjustable-speed drive, allowing for a wider flow range without wasteful recycling
• Good suction-lift capabilities that can maximize line-stripping operations while being able to tolerate the intake of entrained air and other gases without vapor locking
• High volumetric and overall operating efficiencies, resulting in reduced operational costs
• Production of high and constant flow rates even when exposed to upstream and downstream pressure fluctuations, ensuring consistent loading and unloading times
• Low internal velocities
• Low mechanical vibration that lengthens service life
• Intrinsically smooth and quiet operation
• Extremely low pulsation reduces stress and prolongs life of associated fluid-transfer components (piping, hoses, etc.)
Recognizing the operational advantages that can be achieved when installing and using screw pumps in fluid-transfer applications on ships, tankers and barges, Blackmer
®, Grand Rapids, MI, USA, a leading provider of pumps and compressors for industrial use, and a product brand of PSG
®, Oakbrook Terrace, IL, USA, a Dover company, has developed the S Series Screw Pump product line.
Specifically, Blackmer recommends that two of its S Series pump models be considered by shipbuilders – Twin Screw With Timing Gear (WTG) and Triple Screw.
The Twin Screw (WTG) pumps have been designed with external bearings and a timing-gear transmission, which produces double-suction, self-priming operation with no metal-to-metal contact between the pump’s internal components. This design helps the Twin Screw (WTG) pump achieve the highest flow rates of any rotary PD pump, even at varying backpressures and viscosity levels. In fact, the deliverable flow rate of a PD screw pump, unlike a centrifugal pump, actually increases as the fluid’s viscosity increases. These design characteristics also make screw pumps suitable for all types of transfer applications, including low- or high-viscosity, lubricating or non-lubricating, neutral or aggressive, and clean or contaminated fluids. These features make the Twin Screw WTG pumps ideal for use in loading/unloading and cargo-transfer activities on VLCCs, product tankers and barges.
The Triple Screw pumps are made to handle clean lubricating fluids without solid content across a wide range of viscosities, temperatures and pressures. They are designed with a male drive spindle, two female secondary spindles and a case that contains the screws, which allows the fluid to move smoothly and continuously in an axial direction from suction to discharge. This method of operation delivers smooth, constant product flow with low noise and high levels of energy efficiency. As such, the Triple Screw pumps are a perfect choice for use below decks in the engine room as lube-oil and diesel-injection pumps for all classes of tankers, as well as the vessels that serve and supply them. Both models offer optional double mechanical seals as a way to eliminate an ignition source and to safeguard against process-fluid discharges. The result is pumps that are safer for site personnel, the ship, tanker or barge, surrounding areas and the environment.
Conclusion
To say that VLCCs and ULCCs are simply “large” is an obvious understatement. While supertankers and product tankers play an integral role in the global economy, the success of their operations can only be ensured if the pumps that are used to load and unload them can be counted on to perform reliably and efficiently while handling many thousands of gallons of different types of crude oil-related fluids. While centrifugal pumps have been a first choice for these operations for many years, a better option can be twin or triple screw pumps.
Though screw pumps may have a higher purchase cost than centrifugal pumps, it’s best to remember this old bromide: “buying cheap just means you’ll have to buy it again.” Besides that, the main operational advantages that screw pumps have – the ability to handle a wider window of fluid viscosities at higher rates and pressures, lower energy consumption and no BEP to deal with – leave them poised to become a more efficient, reliable and versatile alternative to centrifugal pumps for shipbuilders who must outfit their fleets.
About the Author:
Josh Pepper is the Global Product Manager – Screw Pumps for Blackmer
®, Grand Rapids, MI, USA, and can be reached at (616) 248-9235 or
josh.pepper@psgdover.com. For more information on Blackmer’s full line of pumps and compressors, please go to
blackmer.com or call (616) 241-1611. Blackmer is a product brand of PSG
®, a Dover company, Oakbrook Terrace, IL, USA. PSG is comprised of several of the world’s leading pump brands, including Abaque
™, Almatec
®, Blackmer
®, Ebsray
®, EnviroGear
®, Griswold
™, Mouvex
®, Neptune
™, Quattroflow
™, RedScrew
™ and Wilden
®. You can find more information about PSG at
psgdover.com.
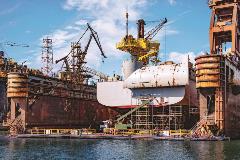
Shipbuilders have long outfitted their vessels with centrifugal pumps that would be used to unload, offload and transfer liquid cargo, but they would be wise to consider the operational benefits that positive displacement screw pumps can offer. Blackmer
® has developed its S Series Twin and Triple Screw Pumps to reliably, efficiently and cost-effectively handle liquids at the high volumes and varying viscosities that are common in the shipping industry’s oil-and-gas transfer applications.
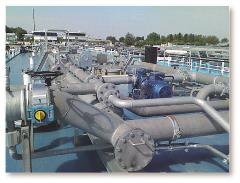
With capacities of up to 550,000 dead weight tons, the shipping industry’s very large crude carriers (VLCC) and ultra large crude carriers (ULCC) require pumps that can reliably manage the high flow rates that are needed to complete a loading or offloading operation.
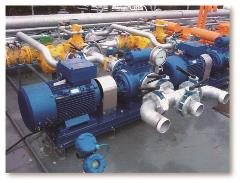
Twin and Triple Screw Pumps from Blackmer
® have been designed to fit in the tight below-decks confines that are common on many types of ships that are used to transport liquid cargo around the world.
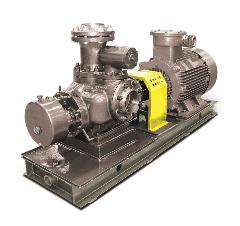
Blackmer S Series Twin Screw Pumps with Timing Gear (WTG) have been designed with external bearings and a timing-gear transmission, which produces double-suction, self-priming operation with no metal-to-metal contact between the pump’s internal components. This design helps the pump achieve the highest flow rates of any rotary PD pump, even at varying backpressures and viscosity levels.
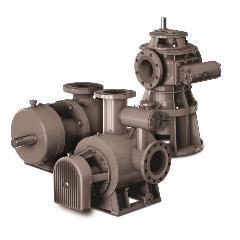
Realizing the many different types and volumes of fluids that must be handled at high flow rates in liquid terminals, Blackmer offers a complete family of highly efficient and versatile twin and triple screw pumps.