NEXT-GENERATION AIR DISTRIBUTION SYSTEMS (ADS) CAN REDUCE AIR CONSUMPTION, LEADING TO IMPROVED EFFICIENCY AND REDUCED OPERATING COSTS
By Erik Solfelt
Success for industrial operations around the world can be measured in a number of different ways, such as Operational Equipment Efficiency (OEE), productivity and safety, to name a few. Almost always they can be grouped into one of three categories: Keeping operating costs low, keeping customers happy and keeping employees safe. Happy customers and safe employees are typically easy to identify and measure for most industrial plants. However, operating costs tend to have hidden components that are not so easy to spot.
In the industrial sector, some of the most significant operational costs – whether in the chemical processing, food and beverage, oil and gas, pharmaceutical or mining industries – are the ones incurred for the purchase, operation and maintenance of pumps used during various production and transfer processes.
One of those hidden components from the operating-cost perspective can often be the electricity used by pumping systems, which, according to a Hydraulic Institute study, account for nearly 20% of the world’s electricity demand. Assuming 7 cents per kilowatt/hour, that equates to approximately $294 billion. Therefore, it’s not surprising that energy consumption can make up close to 90% of the total life-cycle cost of owning and operating a pump.
It has also been estimated that 30% to 50% of the energy that is consumed by pump systems can be saved through equipment or control-system upgrades. Taking all of these usage estimates into consideration, simple arithmetic tells us that up to $147 billion of electricity costs will either go to the industrial companies or the energy provider.
Since pumping systems are ever-present in almost all industrial manufacturing facilities and are crucial to the operation of many production applications across a wide array of industries, they are also ripe for operational improvements that can decrease energy consumption, resulting in both lower operating costs for the facility manager and a more environmentally friendly carbon footprint.
This article will show how recent improvements in air-operated double-diaphragm (AODD) pump technology are helping industries around the globe reduce air consumption, which delivers many significant benefits for both the operator and the environment.
The Challenge
The two main challenges for industrial manufacturers with fluid-transfer operations are the fact that all pumping systems, no matter the technology that is deployed, can be operationally improved in some way so that they are more efficient and cost-effective to operate. Secondly, speaking specifically of AODD pumps, there can be hidden electricity costs related to air consumption that are hard to quantify because those costs can be included in the expenses needed to operate other equipment in the plant.
Upon its invention more than six decades ago, AODD pump technology became an immediate sensation in the industrial-manufacturing sector. AODD pumps are the best solution for many applications because of their simple design, which allows the displacement of a regulated amount of fluid from one of its two liquid chambers upon the completion of each pumping stroke. AODD pumps also feature only a few wetted parts that are dynamic: their two diaphragms, which are connected by a common shaft, the two inlet valve balls and the two outlet valve balls.
Driving the diaphragms with compressed air instead of the shaft balances the load on the diaphragm, which removes mechanical stress from the operation and extends diaphragm life. This also allows the valve balls to open and close on the valve seats, which direct liquid flow. This uncomplicated design and operation makes it easy for the operator to find the correct pressures and flows to optimize the AODD pump’s operation.
This makes AODD pumps ideal for use with a number of different types of liquids, from crude oil and paints to cooking sauces and shampoos.
The design of the AODD pump, though, could leave its operation susceptible to higher rates (and corresponding costs) of compressed air usage. Namely, the earliest air distribution systems (ADS), which are the AODD pump’s motor, would, at the completion of each stroke, produce a moment where a small but still notable amount of compressed air would be allowed to “overfill” the air chamber without any corresponding displacement of fluid. Think of this overfilling as being similar to hitting the gas pedal in an automobile while driving over a patch of ice; the wheels may spin, but the vehicle doesn’t move forward, which is ultimately a waste of gas or energy.
Knowing this, the search was on to develop an ADS that could reduce the rate of air consumption in relation to the product flow rate while also minimizing the overall amount of wasted air that is not enhancing product yield during the pumping cycle. If realized, this type of ADS would positively impact an operation’s bottom line through improved production rates with reduced compressed-air consumption.
While some notable enhancements to ADS performance did occur over the years, the troubling problem of wasted air continued to be observed at the conclusion of each pumping cycle. What was needed was a true game-changer in this realm of AODD pump air consumption.
The Solution
In 2013, Wilden
® Pump & Engineering Company debuted a new solution for this industry challenge with the release of its revolutionary Pro-Flo
® SHIFT Air Distribution System. The operation of the Pro-Flo SHIFT was not just an incremental improvement in ADS technology, but a true revelation, one that presented an entirely new way of looking at how AODD pumps operate and consume air.
To combat the inefficient use of air, the Pro-Flo SHIFT restricts air flow into the air chamber near the end of each pump stroke so that only enough air is introduced to keep the pumping process going. This is accomplished through the incorporation of an innovative air control spool that automatically meters the air to prevent overfilling with no reduction in product-yield rates. The result is reduced air consumption while maximum operational efficiency and flow rates are maintained. This means that, in many cases, the Pro-Flo SHIFT can reduce air consumption by 60% when compared to the operation of competitive ADS technologies, all while retaining desired flow rates.
In addition, the automatic efficiency gains of the Pro-Flo SHIFT eliminate the need for the operator to manually dial in the efficiency or to control it with an expensive electrical system. This creates an improved efficiency point in AODD pump operation with no loss of flow rate. The Pro-Flo SHIFT also delivers extraordinary maintenance advantages as it minimizes wear and tear on the diaphragms during operation through the optimization of every pump stroke.
Additional benefits of the Pro-Flo SHIFT ADS include:
• Reduced total cost of ownership
• Faster setup time
• Ease of maintenance
• Drop-in configuration capability
• Ability to be retrofitted into existing Wilden AODD pumps
• Ability to be used in harsh operating environments
• No electricity required • Completely submersible
• Environmental sensitivity
The Pro-Flo SHIFT’s ability to not only reduce and optimize air usage, but also maintain or even improve flow rates, can save the plant operator the cost of purchasing new pump equipment or compressed-air systems. The simplest way to increase a plant’s production capacity may be to simply switch out the ADS in the existing AODD pumps with the most current ADS technology rather than buying new or additional pumping units.
Conclusion
For industrial operations, there will always be built-in costs of doing business. To mitigate these costs, it is important to recognize what the inherent expenses are and find ways to streamline them in order to create a more profitable business. While those industries and facilities that rely on AODD pumps for their production and product-transfer operations are taking advantage of a cutting-edge, reliable, efficient and environmentally friendly pumping technology, they can only realize the ultimate benefits of that technology if they are optimizing their air usage.
Wilden’s Pro-Flo SHIFT next-generation ADS technology effectively eliminates the problem of wasted air during the pump’s operation. This ability results in optimized operating costs and a healthier bottom line for the facility operator.
About the Author:
Erik Solfelt is the Diaphragm Pump Product Manager for Wilden® and PSG®. He can be reached at (909) 422-1741 or Erik.Solfelt@psgdover.com. Based in Grand Terrace, CA, USA, Wilden is a leader in air-operated double-diaphragm (AODD) pumps and a product brand of PSG®, a Dover company, Oakbrook Terrace, IL, USA. PSG is comprised of several leading pump companies, including Abaque™, Almatec®, Blackmer®, Ebsray®, EnviroGear®, Griswold™, Mouvex®, Neptune™, Quattroflow™, RedScrew™ and Wilden®. You can find more information on Wilden at wildenpump.com and on PSG at psgdover.com.
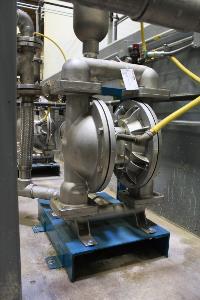
Advanced Air Distribution System (ADS) technology can reduce the operating costs for air-operated double-diaphragm (AODD) pumps in a number of industries, including chemical processing, food and beverage, oil and gas, pharmaceuticals and mining.
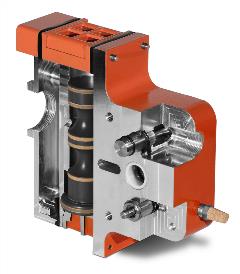
The design and operation of the Pro-Flo
® SHIFT Air Distribution System (ADS) from Wilden
® represents a revolutionary leap forward in optimizing the rate of air consumption in air-operated double-diaphragm (AODD) pumps.
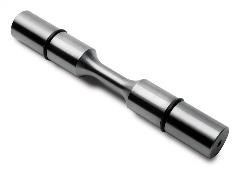
The incorporation of an innovative air control spool into the design of the Pro-Flo
® SHIFT ADS is what gives it the ability to arrest air loss at the conclusion of each pumping stroke, which helps make the Pro-Flo SHIFT up to 60% more efficient than competitive ADS technologies.
.tmb-medium.jpg?Culture=zh&sfvrsn=db3e3786_2)
The performance of AODD pumps can become more cost-effective through the use of advanced ADS technology that reduces the amount of air that is wasted, resulting in lower utility and overall operating costs.
[sidebar] Controlled Comparisons
To create real-world conditions to measure the effectiveness of various ADS technologies industry-wide, a controlled, objective head-to-head test was arranged comparing the industry’s top AODD pumps that have been fitted with traditional, electronically controlled and mechanically actuated ADSs. Common conditions of service that are seen in the field were replicated in the laboratory. This simulated application required each pump to produce a flow of 320 liters per minute (L/min) (85 gpm) against a head pressure of 2.1 bar (30 psi). To achieve a fair comparison between these competing pumps, each pump was run at the inlet air pressure needed to meet the common condition of service. Air-consumption data was then recorded.
The data gathered in the objective AODD testing shows conclusively that Pump D (Wilden
® Pro-Flo
® SHIFT) beats the competition in all three key points of measurement with the lowest air consumption in standard cubic feet per minute (SCFM), the lowest strokes per minute and the highest volume of fluid pumped per SCFM. Pump D averages an overall 30% reduction in air consumption compared to Pumps A, B and C. It also manages the largest reduction in air consumption among the four pumps while still managing the best overall volume of fluid moved per stroke, requiring the lowest strokes-per-minute.
To combat the phenomenon of overfilling, the Pro-Flo SHIFT restricts the air flow into the filling air chamber at the end of the pump’s stroke to minimize the compressed air that is wasted. The revolutionary air control spool of the Pro-Flo SHIFT meters the air to prevent overfilling with no reduction in product yield. The result is reduced air consumption while still maintaining maximum operational efficiency and flow rates. Compared to the electronic ADS solution, which requires an electrical power source and the delayed “learning” period after each startup, the Pro-Flo SHIFT, with no electrical power requirement or delay needed to achieve peak operation, clearly makes choosing the best AODD pump an easy decision.
View the Video - See the Proof
To view the video documenting the laboratory pump demonstration of the Wilden Pro-Flo SHIFT versus the industry’s top competitors, visit
profloshift.com/proof.
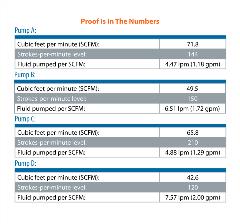