SELECTING THE PROPER FEED AND FILTRATION EQUIPMENT CAN ENABLE OPERATORS TO OVERCOME THE CRITICAL CHALLENGES INHERENT IN THE OPERATION OF CLOSED-LOOP HEATING AND COOLING-WATER SYSTEMS
By Jay Farmerie and Tom O’Donnell
There are a few perfect things in this world – a baby’s smile, beachfront sunsets and a pitcher who retires 27 consecutive batters come to mind – but unfortunately for those who operate commercial or industrial facilities, hot-water heating, process loops or closed-loop cooling-water recirculation systems are not one of them.
Car radiators may be the closest thing to the perfect closed loop, but even they can have glycol leaks, various metallurgies, air ingress from the expansion tank, temperature excursions (hot to cold, cold to hot) and debris in the system. All of these conditions can lead to severe issues in the system and require corrective actions. This is why the car manufacturers recommend changeout of the glycol after 60,000 miles and every 30,000 miles thereafter.
This cannot be done in a facility’s closed loop, though, which is one of the reasons why commercial and industrial closed-loop systems need to be chemically treated to prevent scale, corrosion and biological growth. Part of that treatment includes the ability to add corrosion inhibitors to the equipment, with integral filtration also being a very big part of that equipment.
This white paper will identify both the traditional and next-generation challenges that affect the capabilities of closed-loop systems used by operators of industrial and commercial facilities (generally with capacities between 100 and 10,000 gallons). It will also highlight how the implementation of filter feeders can enable those systems to operate at their most efficient, cost-effective and reliable best.
The Challenges
Closed loops are becoming a more important part of facility operations since they can enhance heat transfer and conserve water. Ensuring the efficient operation of a closed-loop liquid-recirculation system requires identifying and overcoming challenges, both old and new. The first challenges are as old as the development of the closed-loop system itself:
• Ensure that the heat-exchange properties of the system are maintained
• Make certain that the fluid used to facilitate heat transfer reacts well with the system’s metallurgy to prevent corrosion
• Ensure contaminants in the fluid do not lay out on the heat-transfer surfaces, which will prevent them from providing proper heat transfer
• Ensure that particulates that can damage the internals of the system or foul/plug the system are kept out of the system
• Keep biological growth under control to prevent fouling and corrosion
Another challenge is today’s energy-efficient equipment, such as plate-and-frame heat exchangers and other heat exchangers with very small fl ow orifices or enhanced tubes. These design changes allow more rapid heat exchange and also change the fl ow dynamics of the systems. In the past, we were dealing with mostly shell-and-tube heat exchangers, but with the recent changes in the heat exchangers, engineers are trying to exchange heat very rapidly, so the footprint is smaller.
However, it doesn’t take much to clog up these smaller fl ow orifices. The system’s main piping may not get clogged, but the heat-exchanger surfaces can get clogged with any type of dirt and debris. Any particles that collect on the heat exchanger will also attract other particles to the heat-exchanger surfaces, which in turn kills efficiency and can increase corrosion due to under-deposit corrosion mechanisms, leading to an increase in the amount of solids in the system.
Metallurgies are changing at the same time, which also affects the overall dynamics of the system. Aluminum is one of those new metallurgies that promote rapid heat exchange.
What Is A Closed Recirculating Loop And What Are Its Issues?
First, all closed-loop systems are basically designed like the following diagram:
The diagram is a basic closed loop, but in today’s world the dynamics of these systems are getting more complicated.
Second, a true closed loop is defined as one that loses less than 1% of the fluid it holds in a month. (Example: For a 500-gallon system, that is five gallons. For a 10,000-gallon system, that is 100 gallons.) Anything else would be considered an open recirculating loop. However, many systems in today’s facilities can experience fluid loss of up to 5% per month or greater. Thus, it is very important to know how much water your system is making up per month; having a water meter to measure your system’s water loss is very important.
What is so important about water loss in a closed-loop system? New supply (makeup) water brings in not only the dissolved minerals that are normally in the water, but also oxygen and sometimes even suspended solids and bacteria. The makeup water may be municipal drinking water; however, municipal potable drinking water can contain up to 500 cfu/ml of heterotrophic bacteria, though it cannot contain any coliforms. Suspended solids can be in the water, too, and can produce color and turbidity issues. These solids can include aluminum sulfate, aluminum silicate, iron oxides and other compounds that are all quite prevalent in drinking-water systems.
Where does the water loss come from? It can be a result of pump seals that leak or a drip leak somewhere else in the plumbing or distribution system, or a small fitting or valve that could also be leaking, or even a dripping relief valve. There can also be purposeful leaks or process blowdown that is used to limit other issues in the system. In open-top or vented expansion tanks this loss can also be due to some evaporation. All of this requires replenishment of the lost liquid with new water or fluid. As stated, new water brings with it new oxygen, which means increased corrosion in the system. One may think you have a closed-loop system and that once you put water in it, there will be a little bit of corrosion and then it will stop. But it does not work that way because the corrosion process forms solids and deposits in the system. These deposits can increase corrosion through other mechanisms.
An expansion tank can also be a source of air/oxygen ingress. Most systems today utilize bladder tanks that reduce the air ingress but these tanks do leak small amounts of air into the closed loop during the expansion and contraction process, similar to how a tire loses air over time. Air-blanket tanks (like the ones found in vehicles) and closed loops with open sumps that are open to the atmosphere are also utilized. Thus, an expansion tank can be a source of extra air ingress, allowing air into the system and leading to corrosion.
Today, various metallurgies are also quite common. In the past, most systems just had copper, brass and iron, but today’s systems can include many different metallurgies, including iron, copper, brass, aluminum, stainless steel, nickel, galvanized steel and other metallurgies from plated parts or specialty coatings. Most of these new metallurgies are associated with changing heat-transfer demands and are used in the name of energy efficiency. Engineers have been developing new energy-efficient heat exchangers for years, but design engineers who think water is just water don’t understand the properties of water and how minor changes can alter corrosion rates.
These changes in metallurgy mean different corrosion rates and different water/fluid conditions that must be maintained to limit the corrosion on the specific metallurgies. Sometimes these water or fluid-condition limits are much more restrictive for a specific metallurgy and some may even conflict with the other metallurgies in the system. Thus, having a system move outside the limits for one metallurgy can very easily lead to corrosion on another system metallurgy. (Example: Copper-piping corrosion can lead to severe corrosion on an aluminum heat exchanger.)
One other item that is an issue with closed loops is a normal part of the construction phase of any project: pre-cleaning the new system. Corrosion and fouling protection starts with the pre-cleaning of the system. Dirt and debris, mill scale, pipe-cutting oils, pipe-flux agents and other contaminants are all brought into the system during the construction of the system. Flash rusting agents that are utilized to protect the piping and systems after manufacture are also part of the new system even before water is introduced for the first time.
Corrosion can also occur during the hydro-testing process when systems are filled with water to verify the pipe connections and joints are completely watertight. When a leak is found, the system is drained and sometimes not immediately filled again with water. Thus, fl ash rusting or corrosion can occur during these drained periods. Not all specifications call for hydro-testing inhibitors and/or pre-cleaning of the systems before operation, and sometimes because of time constraints some mechanical contractors leave this process until the end and many times just flush the system with water until the water is clear. The following photo shows a filter that had been installed on a water-only flushed system.
Therefore, leaving these materials in a system can be detrimental to the system’s reliability
The Solutions
Let’s start with the newly constructed or refurbished system. All new or refurbished closed loops need to be hydrotested first with a vapor-phase corrosion inhibitor so the systems are protected during the draining and filling phase of the hydrotesting. (Note: The owner of the equipment or system and the engineers should verify that these are included in the new construction specifications.) Based on experience in the field, hydrotesting is normally not done just once as you might expect, but it can be done many times; the more times a system is drained and refilled, the more problems that can occur in the future. Corrosion will occur on the metallurgy because the fill/drain/refill process is similar to constantly dipping a nail into a jar of water, then removing it. It can even be more severe because if all the water is not removed from the piping or system, it becomes like the Amazon jungle in the enclosed piping.
Second, new and refurbished systems need to be pre-cleaned properly. In all new systems, pre-cleaning can utilize normal surfactants and dispersants, but in a refurbished system, you may need to include more aggressive cleaners to remove old deposits and foulants. This may be especially true if used equipment is utilized in the new system. In all parts of this process, filtration should be included as demonstrated in the photo above. During the cleaning process, water testing needs to be done throughout the various steps (before cleaning, during cleaning, during the flushing and after the post-passivation steps).
The testing should calculate many different factors, including water hardness, alkalinity, chlorides, silica, oils and grease, TOC, sulfates, pH, conductivity, and iron, copper and aluminum levels. A particle-size distribution analysis should also be performed on the final flush water or system water because most new energy-efficient equipment providers have limits on suspended solids and the size of the particles. A report should be issued by the company doing the cleaning and testing, discussing the protocol utilized, the testing results and any oddities that occurred that may influence the system later. The report should also include any recommendations for future operation of the system. This report provides verification and certification that the specifications have been followed.
To protect the system during normal operation, corrosion inhibitors should be added to slow down the corrosion rates. (Note: Corrosion can never be totally stopped, its rate can only be slowed.) The corrosion inhibitors must meet the needs of each of the metallurgies involved in the system. Most water-treatment providers combine various corrosion inhibitors to protect various metallurgies in their formulations, but they must verify that their formulations do indeed meet the requirements of the specific system involved and the various heat exchangers and metallurgies included in the system. The water treater should be provided with all equipment submittals to verify that the treatment consists of the proper material for the system.
Most of the blended formulations also include polymeric dispersants to try to keep the suspended solids in suspension. This is where filtration becomes very important in helping to remove any solids left or formed in the system during operation. Traditional methods of removing contaminants have included screen strainers and dirt/air separators. However, such screens are quite large and are approximately 60-mesh, which is equivalent to 250 microns. With the new energy-efficiency equipment, filtration down to 5 microns or lower is a must.
Thus, identifying and utilizing a piece of equipment that combines filtration that can both capture any harmful contaminants and particulates while also possessing the capability to add chemicals that protect against corrosion becomes very important. In fact it is imperative to specify filtration on closed-loop systems. If the system is dirty, you will decrease the efficiency of the heat-exchanger equipment, which results in increased electricity and natural gas costs.
As a solution, many operators began to incorporate separate cartridge filters and bypass feeders into their closed-loop recirculation systems while others combined the systems with a tie-in bag.
With cartridge filters, the fluid goes through the system from the outside to the inside and it does filter the system, but you cannot totally flush out the dirt and debris that the cartridge filter drops on the outside of the filter, so the solids will drop to the bottom of the feeder. Thus, when you restart the filtration, you move the materials back onto the filter if it is installed properly and if it is not, then the material goes back into the system.
The next generation of these combined units became the filter feeder that protects against harmful particles and debris. This is a design that features a filter bag that is used to trap any contaminants that can be completely removed from the system and disposed of. A 5-micron bag filter has been designed to capture impurities that are smaller than the width of a human hair. Another benefit of the filter bag in a filter feeder is that when it becomes full, it can be removed from the filter feeder and thrown away, meaning that all of the solid particles that have been captured are finding their way into the garbage and not being reintroduced to the closed-loop system.
Specifically speaking, Neptune
™ Chemical Pump Co., North Wales, PA, USA, which is a product brand of PSG
®, a Dover company, Oakbrook Terrace, IL, USA, has designed its FTF Series Filter Feeder for use in closed-loop liquid-recirculation systems.
The FTF Series Filter Feeders are available in five models with capacities ranging from 2.5 to 7.5 gallons (9.5 to 28.4 liters). They have been designed to be a convenient way to introduce solid or liquid chemicals into hot- or cold-water closed-loop recirculating systems while possessing the ability to filter out any contaminants that may foul the system, even those as minuscule as 1 micron in size. They feature a stainless-steel perforated basket that holds and fully supports the filter bag inside. One model, the FTF-5150HP, offers oversized 1.5” (38 mm) inlet and outlet connections that allow it to be used for system cleanup with high-volume pumps where high fl ow rates are needed for fast cleanup or a flushout prior to startup.
Significant benefits of Neptune’s FTF filter feeders include:
• Ability to achieve filtration at the same time as chemical injection
• Elimination of the need for a separate bypass feeder and cartridge filter
• Availability of filter bags with 1-, 5-, 20- and 50-micron ratings
• Ability to quickly and easily replace filter bags
• Extended neck with top inlet that allows simple installation of filter bag and basket
• A quick-opening, high-pressure closure that offers better sealing with less force and no need for special tools, while also possessing the ability to inhibit opening under pressure
Conclusion
While closed-loop recirculation systems will never be “perfect,” it is imperative in the era of new high energy-efficiency systems that their operation come as close as possible to that nirvana of performance. High-performance filter feeders that have the capability to both capture and control contaminants and inject the chemicals that help prevent corrosion can play a significant role in optimizing the performance of the closed-loop system.
About the Authors:
Jay Farmerie is an Executive Consultant for Cyrus Rice Water Consultants, Inc., and has been providing water-related consulting and engineering services for clients for more than 35 years. The water-management and consulting services of Cyrus Rice are utilized by the representatives of the heavy and light processing industries, architectural and design engineering fi rms, government agencies, fossil-fuel and nuclear power plants, and public utilities, including municipal water and wastewater-treatment plants. He can be reached at (412) 269-2468 or support@cyrusrice.com. For more information on Cyrus Rice Water Consultants, please visit cyrusrice.com.
Tom O’Donnell is Director of Business Development for Neptune™ and PSG®. He can be reached at (215) 699-8700 or Tom.ODonnell@psgdover.com. Based in North Wales, PA, USA, Neptune Chemical Pump Co., is a leading manufacturer of chemical metering and peristaltic (hose) pumps, chemical feed systems, chemical injection accessories, polymer makedown systems and portable mixers. Neptune is an operating company within PSG, Oakbrook Terrace, IL, USA, a Dover company. PSG is comprised of several leading pump companies, including Abaque®, Almatec®, Blackmer®, Ebsray®, EnviroGear®, Griswold™, Mouvex®, Neptune™, Quattroflow™, RedScrew™ and Wilden®. You can find more information on Neptune at neptune1.com and PSG at psgdover.com.
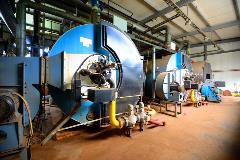
There is no thing as a perfect closed-loop system, which means that such industrial activities as hot-water heating and cooling-water recirculation require assistance in order to prevent the scale buildup, corrosion and biological growth that can foul the system and hamper its operational capabilities. These hurdles can be overcome through the use of filter feeders, such as FTF Series models from Neptune
™ Chemical Pump Co., that possess the ability to reliably, efficiently and cost-effectively perform both chemical-injection and contaminant-filtration functions.
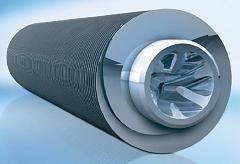
Figure #2 – Photo of enhanced tube from an aluminum boiler system.
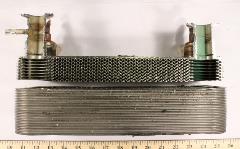
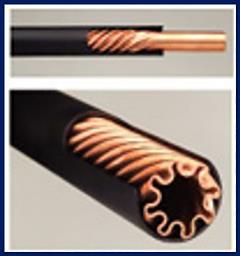
Figure #1 – Photo of enhanced tubes from a heat-pump system (above) and a cross-sectioned plate-and-frame heat exchanger (left).
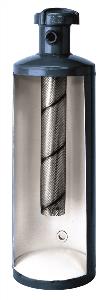
Model FTF-5HP
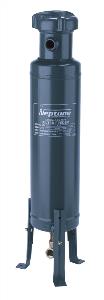
Model FTF-2DB

Stainless-Steel Basket
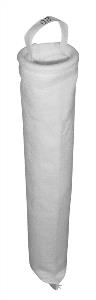
Filter Bag