IMPROVEMENTS IN OPERATIONAL EFFICIENCY COUPLED WITH THE ABILITY TO HANDLE MOST CHEMICALS MAKE THE AIR-OPERATED DOUBLE-DIAPHRAGM PUMP A PERFECT CHOICE FOR CHEMICAL PROCESSORS
By Erik Solfelt
Since its invention in 1955 as a mining pump, the air-operated double-diaphragm (AODD) pump has established a well-earned reputation as a technology that is ideally suited for utilitarian, auxiliary or basic liquid-handling and transfer applications. AODD pumps excel in these types of applications because they possess design characteristics that allow them to offer simple, seal-less operation and enable them to self-prime, run dry, achieve suction lift up to 30 feet (9 meters or 14.7 psia), resist deadhead pumping conditions, operate while submerged and pass solids up to 3 inches (76 mm) in diameter.
It didn’t take long for companies to see why these operational characteristics would be highly desirable in many process applications and why AODD pumps are in actuality true “process” pumps that are capable of performing efficiently, reliably and safely in a wide range of critical fluid-handling applications. AODD pumps also hit the operational sweet spot in many of the fluid-handling tasks that are prevalent in the chemical-processing industry.
In fact, there are four key areas in which AODD pumps will outperform competitive technologies in terms of efficient, reliable and cost-effective operation. Chemical processors who are looking to optimize their operations would be wise to consider the advantages that AODD pumps can provide in these areas. Let’s take a closer look at all four:
1) The Importance of Air
As their name states, the operation of AODD pumps relies on compressed air, which can be found in most chemical-processing plants around the world. Leveraging this ready availability of air can make the AODD pump a true plug-and-play device that requires no infrastructure upgrades to incorporate. Additionally, the use of air to power the pump is the key source of one of its most sought after capabilities, the ability to deadhead without damaging the pump, system or fluid. This makes AODDs very easy and flexible pumps to operate.
Keeping air usage low is critical to maintaining a healthy environment and a healthy processing plant, and recent technological advances have taken significant steps toward realizing these goals. The advances have been focused around one slight shortcoming in AODD pump operation - at the end of every pump stroke, a small amount of air is consumed that does not contribute to the movement of the fluid. (Imagine hitting the gas pedal in a vehicle that is on ice; the wheels spin, but the car doesn’t move.) Because of that operational challenge, the manufacturers of AODD pumps were constantly searching for ways to decrease or eliminate the air (or energy) loss at the end of the pump stroke. AODD pump developers kept working to conquer the air-loss quandary and eventually reached a new pinnacle of ADS operation in 2013 when the engineers at Wilden® Pump and Engineering Co., completed the development of the Pro-Flo® SHIFT ADS technology.
This redesigned ADS features a revolutionary air control spool that reduces the amount of air that is allowed into the pump at the end of the stroke, which drastically reduces the amount of “wasted” energy that had traditionally been lost to the atmosphere. This allows the AODD pump to realize up to 60% savings in air consumption (over competitors), improves the pump’s suction-lift capabilities and enables the pump to better handle high inlet pressures, all while delivering more yield per standard cubic per minute (scfm) of air consumed than AODDs that feature traditional ADS technology.
2) Low Maintenance Costs
Through Proper Diaphragm Selection Diaphragm pumps have a unique benefit when compared to many rotating-pump technologies in that they don’t require any seals. Elimination of the need for packing or expensive mechanical seals means that maintenance costs tend to be inexpensive and infrequent. Combined with the ease of operation, AODDs are a true “set-and-forget” type of pump, provided the right diaphragms are selected for the application. Diaphragm material choice, shape and pump design all play a role in enhancing the life of the diaphragm.
Along with the advances in ADS design and operation, the improvements made in diaphragm construction and function over the years have been meaningful. Chief among them is that long-life diaphragms that have been engineered for use in chemical-processing activities require less maintenance, which lowers repair costs for the operator. Wilden has stepped forward in this area, as well, with the creation of the Chem-Fuse Integral Piston Diaphragm (IPD). Unlike conventional diaphragms, the outer piston in the Chem-Fuse IPD is completely encapsulated within the diaphragm’s thermoplastic (TPE) elastomer material, which provides several benefits.
First, the IPD design removes the phenomenon known as outer piston abrasion, which is when the outer piston rubs against the diaphragm as it cycles and over time, like sandpaper, wears away the material. Removing the outer piston eliminates this failure mode, therefore dramatically increasing diaphragm life. Secondly, it also removes a known leak point in traditional diaphragm designs around the outer piston, improving overall safety when handling dangerous chemicals. Finally, the IPD eliminates an area along the outer piston where pumped fluid can be trapped. In summary, with the Chem-Fuse diaphragm, Wilden has been able to create an advanced IPD that uses the same length shaft as conventional diaphragms, so operators can get all of the product-containment, safety and lifetime benefits without sacrificing flow, suction lift or efficiency.
In the end, the downtime and maintenance that unplanned failures can incur are typically more expensive for the facility operator than the spare parts required to keep the AODD pump operating. The use of IPDs allows the pump to run longer before requiring diaphragm maintenance and will translate directly to a healthier bottom line.
3) Versatile and Compatible
By definition, chemical processing requires the completion of some of the most intricate and complex industrial operations in the world. One of the most crucial operations is the transfer of liquids along the production chain. Due to the importance of the many fluid-transfer operations along the breadth of the chemical-manufacturing chain, facility operators need to identify the best pumping technology for the job. The technology must possess the versatility to perform reliably and efficiently at any number of points in the production hierarchy. AODD pumps can match the supposed advantages of competing pump technologies because of a number of operational advantages:
• They are appropriate for use with high-viscosity fluids and can handle fluids that range from water-like to medium and very viscous liquids
• They can run dry and strip discharge lines without getting damaged; if the pressures get to be too much, the pump will just stop running, but it won’t break
• They are simple devices and their control relies solely on solenoid operators, pump-cycle counters and surge-dampener assemblies
• Their operating costs can be lower when all of the maintenance, accessories and controllers are included, and in many cases their total cost of ownership is lower over their entire operational lifespan when compared to competitive pump styles
Additionally, a new generation of AODD pump styles – highlighted by Wilden’s bolted pump models – have been designed to be direct bolt-to-bolt and pipe-to-pipe drop-in replacements in existing pumping systems. This makes them a cost-effective way to upgrade fluid-transfer performance while simultaneously realizing the benefits inherent in the operation of an AODD pump that features an advanced ADS – reduction in air consumption and expense, optimized product handling and containment, and scaled-back maintenance and replacement costs.
Finally, the design and operation of AODD pumps allows them to transfer a wide range of liquids with varying handling characteristics. One of the most prominent is viscosity, or the thickness of the liquid that is being transferred. The operation of AODD pumps virtually eliminates product slip, regardless of the fluid’s viscosity, since the pump’s ball check valves control fluid transfer. Conversely, gear, screw and lobe pump technologies use fixed tolerances to control slip, which means that they are unable to adequately adjust to viscosity changes.
4) Pump Construction
Quality pump construction is key when handling dangerous chemicals, and using a pump designed with the right materials is important to the safety of a plant. To satisfy these demands, AODD pumps are available in a wide range of materials of construction in order to meet a variety of chemical-handling needs. Common chemical-pump materials include polypropylene, Kynar®, stainless steel, ductile iron and Hastelloy, with some companies, like Wilden, possessing the capability to offer special materials like super duplex when really unique materials are required to ensure uninterrupted production processes and the safety of plant personnel.
If metal pumps are required, one overlooked material in the chemical-processing world is ductile iron, which works well in both acidic and basic PH application ranges of 4 to 10. Provided that the chemical compatibility is correct, operators who use ductile-iron pumps can realize all of the benefits of stainless steel, but at a lower price point.
Wilden has a range ductile iron pumps available in bolted, seal-less designs. A bolted design can offer the best features for the user since bolted pumps do not, as mentioned earlier, rely on packing or expensive mechanical seals to prevent leaks. In this case, the most important benefit of bolted pumps is their ability to offer the highest level of product containment. This is critical for two main reasons: many raw or finished chemicals are high-value products and any loss through leakage can be detrimental to the operation’s bottom line and, second, most chemicals can be harmful to humans and the environment.
A final benefit is that all Wilden bolted metal pumps also have improved flow paths for increased flow rates. This enhanced flow capability can allow the operator to use, for example, a 1.5-inch pump where a 2-inch model may have been required in the past, which equates into capital-cost savings.
Conclusion
Thanks to its simple yet innovative design, the AODD pump has proven to be able to consistently meet the demands of chemical processors while building a reputation as a go-to pumping technology where basic fluid-transfer capabilities are required. The AODD pump, which possesses a stable of notable operational characteristics, has become a first-choice technology for chemical manufacturers who are searching for a pump that meshes cost-conscious air consumption with reliable production rates.
About the Author:
Erik Solfelt is the Diaphragm Pump Product Manager for Wilden® and PSG®. He can be reached at (909) 422-1741 or Erik.Solfelt@psgdover.com. Based in Grand Terrace, CA, USA, Wilden is a leader in air-operated double-diaphragm (AODD) pumps and a product brand of PSG®, a Dover company, Oakbrook Terrace, IL, USA. PSG is comprised of several leading pump companies, including Abaque™, Almatec®, Blackmer®, Ebsray®, EnviroGear®, Finder, Griswold™, Mouvex®, Neptune™, Quattroflow™, RedScrew™ and Wilden®. You can find more information on Wilden at wildenpump.com and on PSG at psgdover.com.

While plastic pumps are typically a go-to pumping technology in chemical processing, there can be instances where metal pumps are a better choice for the operator. Specifically, bolted, ductile-iron AODD pumps from Wilden
® can meet the needs of the processor through efficient operation and reliable prevention of leaks and cross-contamination, and they do it at a lower price point than stainless-steel models.
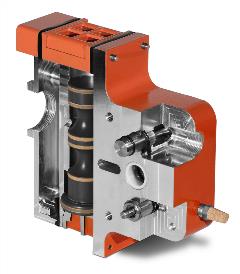
A true innovation in AODD pump operation occurred in 2013 when Wilden
® completed development of its Pro-Flo
® SHIFT Air Distribution System (ADS). The design of the Pro-Flo SHFT, which features a revolutionary air control spool, eliminates costly air loss at the end of the pump stroke, resulting in up to 60% savings in air consumption when compared to competitive models.
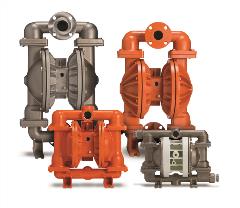
The various models of Wilden
® bolted AODD pumps offer many operational advantages for chemical processors, including optimized flow paths, easy maintenance, quick assembly and disassembly, and the ability to be a bolt-to-bolt and pipe-to-pipe drop-in replacement for competitive pump models.
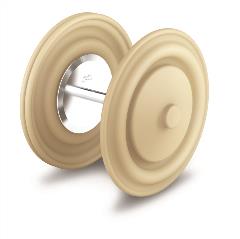
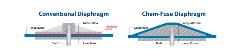
Wilden
® Chem-Fuse Integral Piston Diaphragms (IPD) are designed with a piston that is integrated into the diaphragm itself. The result is that unlike conventional diaphragms, the ChemFuse IPD has no outer piston abrasion, which is a key failure mode for conventional diaphragms, and eliminates a potential leak point around the outer piston. This means improved diaphragm life and peace of mind when handling hazardous liquids.
[sidebar] Putting The Pieces Together
Everyone knows that a chain is only as strong as its weakest link. In the industrial world it can be said that a pumping system used in chemical-processing applications is only as reliable, efficient and safe as its weakest component.
That’s why Wilden
® has devoted so much time and effort to making its many models of air-operated double-diaphragm (AODD) pumps and their components the industry standard for chemical-processing applications. It’s also why Wilden recommends that chemical processors construct their pumping systems with their industry-leading AODD pump, air distribution system (ADS) and diaphragm technologies:
• Bolted Metal AODD Pumps: Feature chemically compatible ductile-iron construction with a reengineered flow path that can increase flow rates by up to 54%. They are direct drop-in replacements for existing models and are designed with fewer fasteners for faster assembly/disassembly for shorter downtime.
• Pro-Flo
® SHIFT ADS: Stainless-steel construction and a revolutionary design allows the AODD pump to achieve up to a 60% savings in air consumption over competitive AODD pump technologies, while providing higher flow rates per scfm. Also costs 50% less to operate than electronically actuated ADS units, is submersible and has fewer operating parts, which reduces maintenance and repair downtime.
• Chem-Fuse Integral Piston Diaphragms (IPD): Chem-Fuse IPDs solve many of the critical issues faced by chemical companies that generally rely on conventional diaphragms. Chem-Fuse IPDs eliminate the potential leak point at the outer piston when pumping critical or dangerous fluids. They also eliminate any outer-piston abrasion for up to six times the diaphragm life, depending on the application, especially when pumping abrasive fluids. Lastly, for faster product changeovers and the prevention of product contamination, Chem-Fuse IPDs are quick and easy to clean.
The inclusion of these components can create a simple and successful equation for the plant operator:
AODD Pumps + Pro-Flo SHIFT ADS + Chem-Fuse Diaphragms = Chemical-Processing Success.