FRENCH MINING COMPANY SABLES ET MINERAUX S.A.S. CHOOSES A NEW PUMPING TECHNOLOGY, THE ABAQUE
™ HD100 SERIES PERISTALTIC (HOSE) PUMP, TO OPTIMIZE ITS WASTEWATER-REMOVAL PROCESS
By Arnaud Laigle
Quick Facts
Company: Sables et Mineraux S.A.S.
Location: Livry, France
Market: Mining Challenge: Achieve continuous-duty transfer of highly viscous wastewater from a gravel-processing facility to a retention area 800 meters away and over an elevation rise of 6 meters
Solution: Abaque
™ HD100 Series Peristaltic (Hose) Pump
Introduction To the perception of many, the mining industry is a rough-and-tumble one, full of all types of digging, dumping, hauling, conveying and grinding, all in a simple effort to “turn big rocks into little rocks.” In reality, the processes that take those big rocks and transform them into small, manageable pieces that become important components in sand, gravel and cement are very precise and must adhere to strict operational guidelines in order to be successful. And since they are removing raw materials straight from beneath the Earth’s crust, the operations must also be conducted in the most environmentally sensitive manner possible.
In France, Sables et Mineraux S.A.S. (English translation: Sands and Minerals), a subsidiary of parent company Quartz Mineraux, is one of the country’s most prominent mining outfits, with its network of quarries dotting the French countryside. In early 2017, Sables et Mineraux opened its newest mining operation near the small town of Livry, which is located about 270 kilometers (165 miles) due south of Paris.
“I am the Maintenance Manager here and responsible for the maintenance department for this facility,” said Olivier Houx, who has worked for Sables et Mineraux for 10 years. “At this plant, we extract and clean the gravel before the sand is used for cement.”
Waste Not, Want Not
The ability to observe the beehive of activity that Houx oversees and conducts every day at Sables et Mineraux’s Livry facility is to take in a finely choreographed ballet with towering diggers, rumbling dump trucks, whining grinders and rotating pumps assuming the roles of the ballerinas.
The production process actually begins a short distance away from the processing facility where diggers crisscross a quarry, removing the desired materials – in this case, white gravel, with the surrounding and unneeded red gravel sent to a discard pile – and depositing them into waiting dump trucks. When full, the trucks haul the gravel to the processing facility where it is dumped into hoppers that dispense it onto conveyor belts.
The conveyors transport the gravel to the grinders in the processing center where it is ground down into a less-course sand and cleaned before it is placed in piles where the sand waits to be loaded onto the trucks of the companies that contract with Sables et Mineraux for the commodity. When the Livry facility opened, an average of two trucks a day arrived to haul away the sand, but as of June, a steady stream of 20 to 25 trucks a day were flowing into and out of the facility, or roughly three an hour.
The sand-cleaning stage is a critical one in the production process. Simple water is used to the wash the sand, but after it is used, the water is full of “fines” and must be disposed of. From the grinding facility the wastewater is pumped to a 10-meter (33 feet) wide by 2-meter (7 feet) high holding tank where a clarifier is added. This enables a highly viscous, fine-laden slurry to settle to the bottom of the tank, while the cleaner water at the top of the tank is pumped back to the grinding facility to be reused.
Finding the ideal technology to pump the viscous slurry out of the holding tank and into a retention pond some 800 meters (2,625 feet, or half-a-mile) away over a total elevation rise of 6 meters (20 feet) was a challenge that needed to be overcome when the facility was designed. At most of its other facilities, Sables et Mineraux has used progressive cavity pumps for wastewater disposal, but they did not possess the muscle to adequately transport the water over both the distance and elevation rise that were a defining challenge at the Livry facility.
A Change In Direction
As an alternative, Sables et Mineraux agreed to try a 100-mm (4”) HD100 Series Peristaltic (Hose) Pump from Abaque
®, a pump technology manufactured in Europe by Auxerre, France-based Mouvex®, for its wastewater-disposal duties. Both Abaque and Mouvex are product brands of PSG
®, a Dover company.
“They had been using progressive cavity pumps, but they were only able to pump 3 or 4 meters (10 to 13 feet), and they were also failing too often,” explained Arnaud Laigle, Abaque Product Manager. “They had not been familiar with peristaltic pumps, so we suggested they switch to the Abaque pump because it can pump longer distances through good suction lift, is self-priming and can run dry, and they also won’t stall, like a progressive cavity pump, if the slurry becomes too thick.”
The secret to the HD100 Series pump’s success in this application for Sables et Mineraux is a pumping action that is created by the compression of a circular loop of elastomeric hose through two diametrically opposed shoes. This rotational motion forces the fluid in the hose to move forward of each shoe. When each shoe reaches the top of the loop, the hose immediately returns to its original shape, which ensures suction and priming and creates a strong vacuum that pulls more of the liquid inside.
The Peristaltic (Hose) Pump Operating Principle Peristaltic pumps are also seal-less, which makes them leak-free, a strong consideration when handling wastewater that may contain abrasive, aggressive or viscous fluids. In particular, the HD100 Series pump can produce a maximum discharge pressure of 16 bar (232 psi), handle viscosities up to 63,000 cPs (291,300 SSU) and has a maximum rotation speed of 30 rpm. To fit the needs of the specific application, hoses are available in nitrile rubber (NR), nitrile Buna rubber (NBR), NBR with FDA liner, Hypalon
® and EPDM.
In other words, the HD100 Series is the perfect pump for the needs of Sables et Mineraux. Since its installation, the HD100, which is also outfitted with a pulsation dampener to protect against product surges that can damage the discharge piping, has performed continuous duty consisting of 16 hours a day, five days a week. At peak operating levels, the pump will transfer upwards of 35 to 40 m3/hr (154 to 176 gpm) of viscous wastewater to the faraway retention pond. And it has done it without suffering any service interruptions that would hamper the facility’s production schedule.
“That Abaque pump moves the mud a long way, and even if the pump runs dry, it doesn’t get damaged,” marveled Houx. “We’ve only had to change the hose and the oil inside the pump once this first year.”
Conclusion
Though it may look rough and tumble, the mining process is one that requires every production stage to work in complete harmony and without fail if the final end-product is to be manufactured in a timely, safe and satisfactory way. This includes the disposal of the wastewater that is created during the sand-cleaning process – and with an eye toward environmental stewardship and protection, once the slurry settles in the Livry facility’s retention area, the clean water at the top of the pond is reclaimed and pumped back to the processing facility for reuse.
To meet their needs in this area, Houx and Sables et Mineraux were open-minded enough to turn to a technology they were not familiar with – the Abaque HD100 Series Peristaltic (Hose) Pump – and they could not be more pleased with the results so far.
“We are very satisfied with the Abaque pump because it is very robust and heavy-duty; we needed a pump like that and the Abaque pump is perfect for us,” concluded Houx.
About the Author:
Arnaud Laigle is the Abaque® Product Manager for Mouvex® and PSG® and can be reached at +33 386 49 86 91 or arnaud.laigle@psgdover.com. Auxerre, France-based Mouvex was incorporated in 1906 and is a leading manufacturer of positive displacement pumps, screw compressors and hydraulic coolers for use in the refined-fuels, oilfield, energy, food/ sanitary, military, transport and chemical-process industries, and is a product brand of PSG®, a Dover company. Headquartered in Oakbrook Terrace, IL, USA, PSG is comprised of several leading pump brands, including Abaque®, Almatec®, Blackmer®, Ebsray®, EnviroGear®, Griswold™, Mouvex®, Neptune™, Quattroflow™, RedScrew™ and Wilden®. For more information on Mouvex or PSG, please go to mouvex.com or psgdover.com.
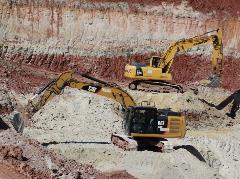
The mining operation at the Sables et Mineraux facility in Livry, France, begins when heavy equipment extracts the desired white rock from the quarry, with the resulting sand used as a component in cement. Disposing of the wastewater created during the cleaning process is a critical operation, and the company has optimized that wastewater-removal process through the use of an Abaque
® HD100 Series Peristaltic (Hose) Pump.
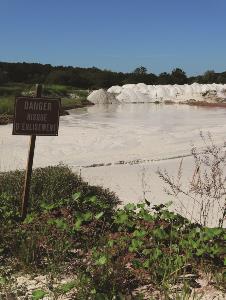
The highly viscous nature of the wastewater at the Sables et Mineraux mine is attested to by the warning sign at the facility’s retention area: “Danger: Risk of getting bogged down” it reads, an admonition to avoid stepping into the quicksand-like substance.
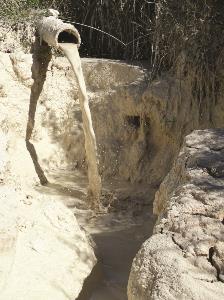
After traveling 800 meters, or half-a-mile, the muddy wastewater is discharged into a retention pond. After the mud settles, the clean water at the top of the pond is reclaimed and reused in the mining process, which helps satisfy the mine’s goal to operate in an environmentally safe and sensitive manner.
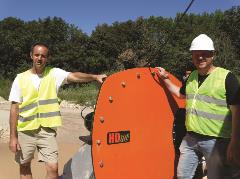
Maintenance Manager Olivier Houx, left, was unfamiliar with peristaltic (hose) pump technology and the potential benefits it could have for the Sables et Mineraux facility until he was introduced to it by Arnaud Laigle, Abaque
® Product Manager, in 2017. Now, after one year of reliable and trouble-free operation, Houx says the Abaque HD100 Series pump “is perfect for us.”
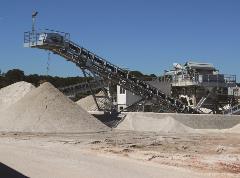
The processing center at the Sables et Mineraux facility turns “big rocks into little rocks” and relies on an Abaque
® HD100 Series Peristaltic (Hose) Pump to dispose of the wastewater that is created during that process.